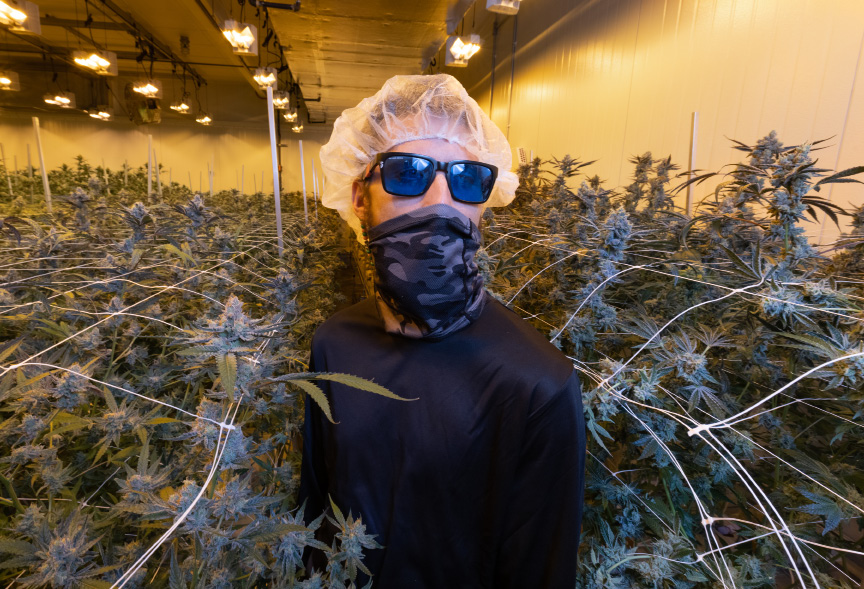
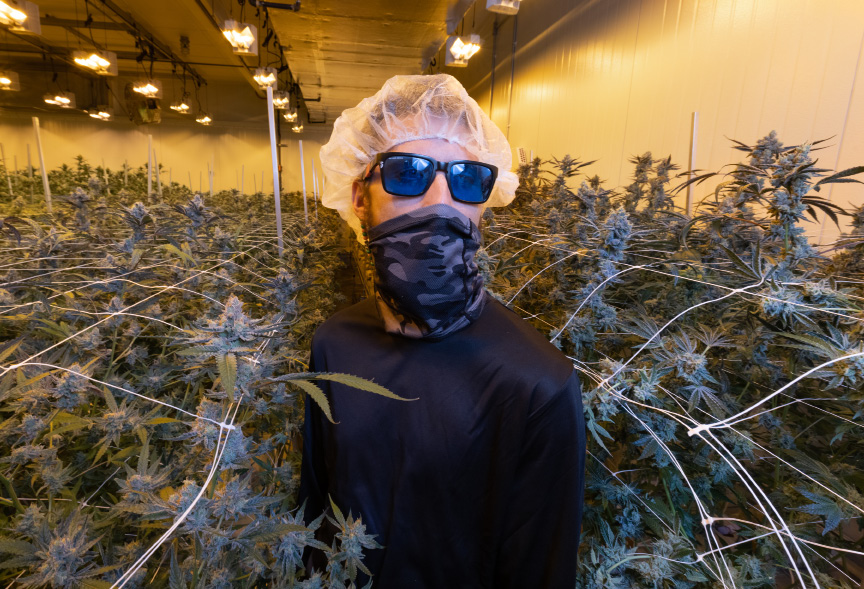
Dressed in medical scrubs and a hairnet, Curaleaf Senior Cultivation Manager Adam Raleigh surveyed a sterile, brightly-lit “flower room” filled with rows of maturing cannabis plants, as the overwhelming smell of marijuana created a thickness to the air.
Equipped with millions of dollars worth of lighting, temperature control and other infrastructure, the Massachusetts-based company’s Simsbury grow operation is a well-honed modern manufacturing facility.
Raleigh said all the high-end equipment Curaleaf uses allows the company to specify and automate the grow process in order to ensure quality while producing at scale.
“[The equipment] affords us the luxury to make sure we’re giving commercial-sized cannabis the attention that it deserves,” Raleigh said. “When you have the tools at your discretion, it does give you the biggest opportunity for success.”
Curaleaf is one of four cannabis producers in Connecticut currently serving the state’s medical marijuana market. But with recreational pot use now legal in the Constitution State, the number of cannabis manufacturers is all but certain to grow, as behemoths like Curaleaf and smaller producers enter the nascent adult-use market.
An inside look at Curaleaf’s Simsbury operations demonstrates to prospective cannabis growers and investors that producing marijuana is an intensive process, requiring high levels of knowledge and a plethora of infrastructure and equipment. It also underscores the challenges that smaller producers will face, in terms of being able to finance the purchase and fit out of a cultivation facility, in trying to enter the state’s recreational market.
“Standing up a grow facility, we’re talking hundreds of thousands, if not millions of dollars, depending on how big you want to go; and it’s going to take probably close to two years,” said Patrik Jonsson, Curaleaf’s regional president of the Northeast.
Offbeat vibes
When you first walk into Curaleaf’s Simsbury grow facility, the building’s front offices have the look, feel and smell of a standard-issue office building with white, fluorescent lighted hallways leading to an office with a grid of desks in cubicles. Employees and visitors have to pass through locker rooms and change into scrubs, masks and shoe covers in order to avoid accidentally carrying in contaminants.
The long, white-tiled hallways lead to areas that warehouse equipment and house growing plants. There’s another area where workers process, distill and cook cannabis edibles. It has a unique hospital/Costco/Willy Wonka’s Cannabis Factory juxtaposition.
Offbeat vibes notwithstanding, Curaleaf’s Simsbury operation is a serious one, producing cannabis for about 20% of Connecticut’s medical marijuana patients.
Brendon Lasky
The key factors to a successful cannabis harvest that growers must control are water, temperature, light, humidity and carbon dioxide, Jonsson said. He estimates the cost of such controls at about $650 per square foot of a grow facility.
Jonsson said Curaleaf learned the importance of these factors the hard way at the company’s first grow facility in Webster, Mass. Curaleaf launched that site in the summer of 2017, harvesting just three pounds that October. In those early days they ran into several issues.
For example, when they loaded as many plants as possible into two grow rooms, the HVAC system got overwhelmed and couldn’t control the extra humidity, which can create a breeding ground for mold and fungi. Additionally, the plants’ girth depleted the room of carbon dioxide that’s key to a flower’s survival.
That’s why, Raleigh said, Curaleaf’s grow rooms are now equipped with heavy-duty HVAC systems and CO2 tanks, which are monitored by a censored control system that adds heat, cooling and carbon dioxide as needed.
“We’re constantly injecting these rooms with CO2 so that they can photosynthesize and they can make the carbohydrates and sugars that they need to create these medical-grade flowers,” Raleigh said. “Environmental control is of the utmost importance.”
In addition to climate controls — which are set at tropical conditions for early-stage plants, and cooler temperatures for mature ones — light is a crucial factor in a successful grow, Raleigh said. Growing plants need 12 hours of light and 12 hours of darkness each day, he said.
HBJ PHOTO | STEVE LASCHEVER
Equipment in the irrigation room of Curaleaf’s Simsbury cultivation facility.
Precision is key
Massachusetts-based Green Meadows, which grows and sells cannabis to the medical and recreational markets in the Bay State, operates a cultivation facility in Southbridge, Mass., about half the size of Curaleaf’s Simsbury operation, said CEO Bob Patton. The company controls the same elements as Curaleaf — i.e. temperature, light, etc. But Green Meadows only uses LED lights, whereas Curaleaf uses a mix of LED and more traditional high-pressure sodium lights.
“There are two schools of thought on lighting,” Patton said.
LED lights are more expensive to install, but use less electricity and could lead to different state tax rebates, depending on where a facility is located.
Jonsson said Curaleaf is working to increase its use of LED lights to reduce the company’s carbon footprint, but it isn’t ready to rely on them entirely.
“Our stance in general is LED lights are great, they’re the future, but … [the technology is] not there yet,” Jonsson said.
Maintaining a solid water and fertilization system is also something that can make or break a harvest, Patton said. Green Meadows’ “fertigation” system runs fertilizer-containing water to all plants, and is controlled by the same automated system as the lights and HVAC, he said.
Curaleaf’s Simsbury facility has an irrigation room filled with huge sealed plastic drums holding fresh water that feeds into nutrient tanks, and then drips into plants via the system’s irrigation line, said Brendon Lasky, a cultivation manager.
Green Meadows’ equipment and infrastructure cost about $350 per square foot, Patton said. While the six-month-old company is much smaller than Curaleaf, it produces about 80 pounds of cannabis per week, which is a larger operation than what smaller craft-cannabis companies may do.
It’s possible to establish a small grow operation for less money, Patton said, but growing cannabis at a high volume is an intensive and pricey proposition.
“I think you can generally say a grow with a couple hundred square feet of canopy can probably work on a simpler system,” Patton said. “[But] we’re talking here about producing quality cannabis at scale.”